What is the Production Process of Mainstream Capacitor Parameters?
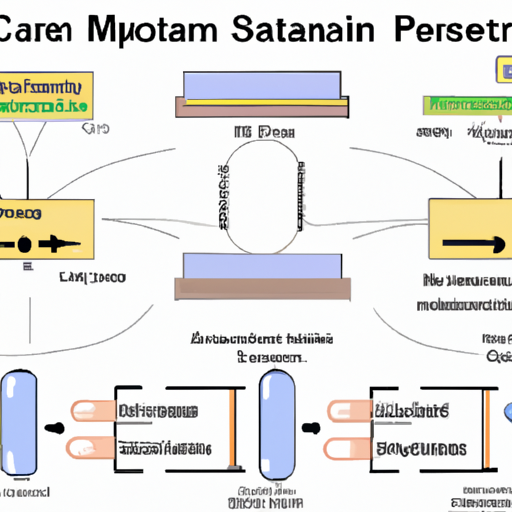
I. Introduction
Capacitors are fundamental components in electronic circuits, serving as energy storage devices that can release energy when needed. They play a crucial role in various applications, from power supply smoothing to signal coupling and decoupling. Understanding the parameters of capacitors is essential for engineers and designers, as these parameters dictate the performance and reliability of electronic devices. This blog post will explore the production process of mainstream capacitor parameters, shedding light on the types of capacitors, their key parameters, and the manufacturing techniques involved.
II. Types of Capacitors
Capacitors come in various types, each with unique characteristics and applications. Here are some of the most common types:
A. Electrolytic Capacitors
Electrolytic capacitors are polarized capacitors that use an electrolyte to achieve a high capacitance value. They are commonly used in power supply circuits due to their ability to store large amounts of energy.
B. Ceramic Capacitors
Ceramic capacitors are non-polarized capacitors made from ceramic materials. They are known for their stability and reliability, making them suitable for high-frequency applications.
C. Film Capacitors
Film capacitors use a thin plastic film as the dielectric material. They are known for their low ESR and ESL, making them ideal for audio and high-frequency applications.
D. Tantalum Capacitors
Tantalum capacitors are another type of electrolytic capacitor, known for their small size and high capacitance. They are often used in compact electronic devices.
E. Supercapacitors
Supercapacitors, or ultracapacitors, have a much higher capacitance than traditional capacitors and can store large amounts of energy. They are used in applications requiring rapid charge and discharge cycles.
F. Comparison of Different Types
Each type of capacitor has its advantages and disadvantages, making them suitable for specific applications. For instance, while electrolytic capacitors offer high capacitance, they may have higher ESR compared to ceramic capacitors, which are more stable but typically have lower capacitance values.
III. Key Parameters of Capacitors
Understanding the key parameters of capacitors is essential for selecting the right component for a specific application. Here are some of the most critical parameters:
A. Capacitance
1. **Definition and Units**: Capacitance is the ability of a capacitor to store electrical charge, measured in farads (F). Most capacitors used in electronic circuits are in the microfarad (µF) or picofarad (pF) range.
2. **Measurement Techniques**: Capacitance can be measured using an LCR meter, which applies an AC signal to the capacitor and measures the resulting current and voltage.
B. Voltage Rating
1. **Definition and Importance**: The voltage rating indicates the maximum voltage a capacitor can handle without breaking down. Exceeding this voltage can lead to catastrophic failure.
2. **Factors Affecting Voltage Rating**: Factors such as temperature, frequency, and the type of dielectric material used can influence the voltage rating of a capacitor.
C. Equivalent Series Resistance (ESR)
1. **Definition and Significance**: ESR is the internal resistance of a capacitor that affects its efficiency and performance. A lower ESR is desirable for high-frequency applications.
2. **Measurement Methods**: ESR can be measured using an LCR meter or specialized ESR meters that apply a small AC signal to the capacitor.
D. Equivalent Series Inductance (ESL)
1. **Definition and Impact on Performance**: ESL is the inductance that appears in series with the capacitor, affecting its performance at high frequencies. Lower ESL values are preferred for high-speed applications.
E. Temperature Coefficient
1. **Definition and Types**: The temperature coefficient indicates how the capacitance value changes with temperature. Common types include X7R, C0G, and Y5V, each with different temperature stability characteristics.
2. **Effects on Capacitor Performance**: A capacitor with a high temperature coefficient may experience significant capacitance variation with temperature changes, impacting circuit performance.
F. Lifetime and Reliability
1. **Factors Influencing Lifespan**: Factors such as operating temperature, voltage stress, and environmental conditions can significantly affect a capacitor's lifespan.
2. **Testing for Reliability**: Manufacturers conduct various tests, including accelerated life testing, to ensure capacitors meet reliability standards.
IV. Production Process of Capacitors
The production process of capacitors involves several critical steps, from raw material selection to final testing. Here’s a closer look at each stage:
A. Raw Material Selection
1. **Types of Materials Used**: The choice of materials is crucial in determining the capacitor's performance. Common materials include aluminum and tantalum for electrolytic capacitors, ceramic materials for ceramic capacitors, and various plastics for film capacitors.
2. **Quality Control Measures**: Manufacturers implement strict quality control measures to ensure that raw materials meet specific standards, as the quality of materials directly impacts the final product's performance.
B. Manufacturing Techniques
1. **Dielectric Layer Formation**: The dielectric layer is a critical component of capacitors. Methods such as chemical vapor deposition (CVD) and sputtering are commonly used to create thin, uniform dielectric layers.
2. **Electrode Preparation**: The electrodes are prepared using various materials, including aluminum, tantalum, or conductive polymers, depending on the capacitor type.
3. **Assembly of Capacitor Components**: The assembly process involves layering and winding the dielectric and electrode materials to form the capacitor structure. This step is crucial for ensuring the capacitor's performance characteristics.
C. Encapsulation and Packaging
1. **Importance of Protection**: Encapsulation protects the capacitor from environmental factors such as moisture and mechanical stress, which can affect performance and reliability.
2. **Common Materials Used for Encapsulation**: Common encapsulation materials include epoxy resins and plastics, which provide a protective barrier while allowing for heat dissipation.
D. Testing and Quality Assurance
1. **Electrical Testing**: Capacitors undergo rigorous electrical testing to ensure they meet specified parameters, including capacitance, ESR, and voltage rating.
2. **Environmental Testing**: Environmental tests simulate real-world conditions, assessing how capacitors perform under various temperature and humidity levels.
3. **Compliance with Industry Standards**: Capacitors must comply with industry standards such as IEC, UL, and RoHS to ensure safety and reliability.
V. Innovations in Capacitor Technology
The capacitor industry is continually evolving, with several innovations shaping the future of capacitor technology:
A. Advances in Materials
New materials are being developed to enhance capacitor performance, including high-k dielectrics that allow for smaller capacitors with higher capacitance values.
B. Miniaturization and Integration
As electronic devices become smaller, the demand for miniaturized capacitors has increased. Manufacturers are developing integrated capacitors that can be embedded directly into circuit boards.
C. Smart Capacitors and IoT Applications
The rise of the Internet of Things (IoT) has led to the development of smart capacitors that can monitor their performance and communicate with other devices, enhancing energy efficiency and reliability.
VI. Conclusion
In summary, understanding the production process and parameters of capacitors is essential for engineers and designers in the electronics industry. From raw material selection to testing and quality assurance, each step in the production process plays a vital role in determining the performance and reliability of capacitors. As technology continues to advance, the future of capacitor technology looks promising, with innovations that will further enhance their capabilities and applications. By grasping these concepts, design engineers can make informed decisions when selecting capacitors for their projects, ultimately leading to more efficient and reliable electronic devices.
VII. References
1. Academic journals on capacitor technology and materials science.
2. Industry publications detailing advancements in capacitor manufacturing.
3. Standards organizations such as IEC and UL for compliance guidelines.